Cooling Water Treatment
- Programs
- Water Management
- Cooling Water Treatment
Cooling Water Treatment
Certain challenges are inherent to industrial cooling systems. When these challenges are not addressed your company may experience reduced operational efficiency, increased cost, increased water usage and reduced life on your equipment. We want to partner and develop a customized solution that fits YOUR SYSTEMS NEEDS.
First we will start with a system assessment. We ask questions like: Are there any signs of microbiological growth? Are there any flow restrictions? Any signs of corrosion and scale accumulation? Is your water or gas expenses rising rapidly? Would you be open to a training session with your team to mitigate current challenges?
Following that assessment, our team will collaborate with you to offer a customized chemistry solution designed specifically for your system's requirements. This chemical program will assist in preserving clean heat transfer surfaces, offering defense against corrosion, scale formation, and biological fouling.
We will continue to evaluate your systems' needs and develop joint process improvements that will optimize operation efficiency, reduce cost, extend equipment life, and minimize the environmental impact.
Our treatment programs are built to meet the required federal, state, local, environmental and compliance regulations. Speaking of regulations; did you know our team is well versed in Legionella pneumophila control.
LEARN MORE ABOUT OUR PROGRAMS, TODAY.
Here are examples of the types of systems we treat: open recirculating, closed chilled loops, cooling towers, and evaporative condensers.
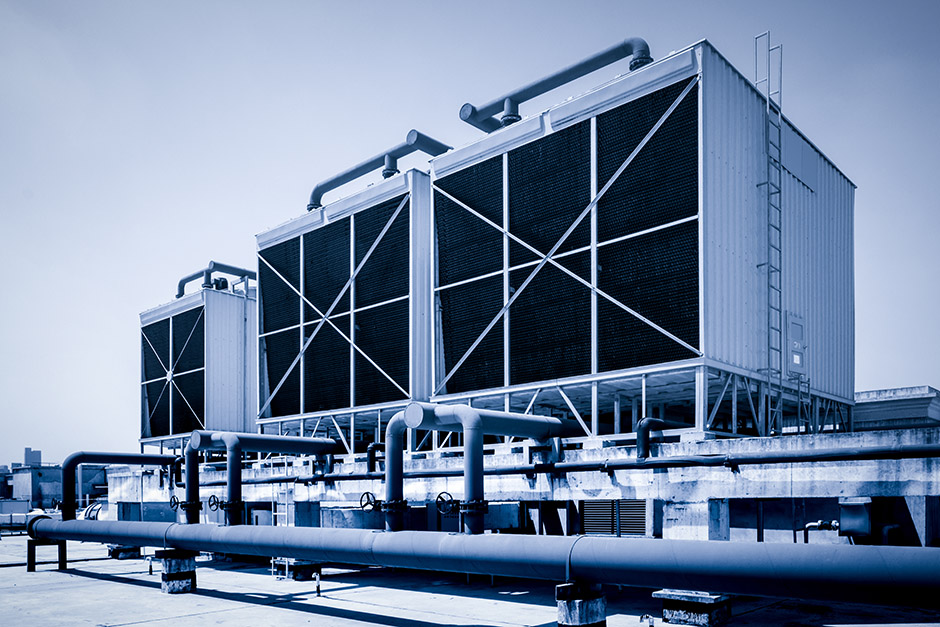
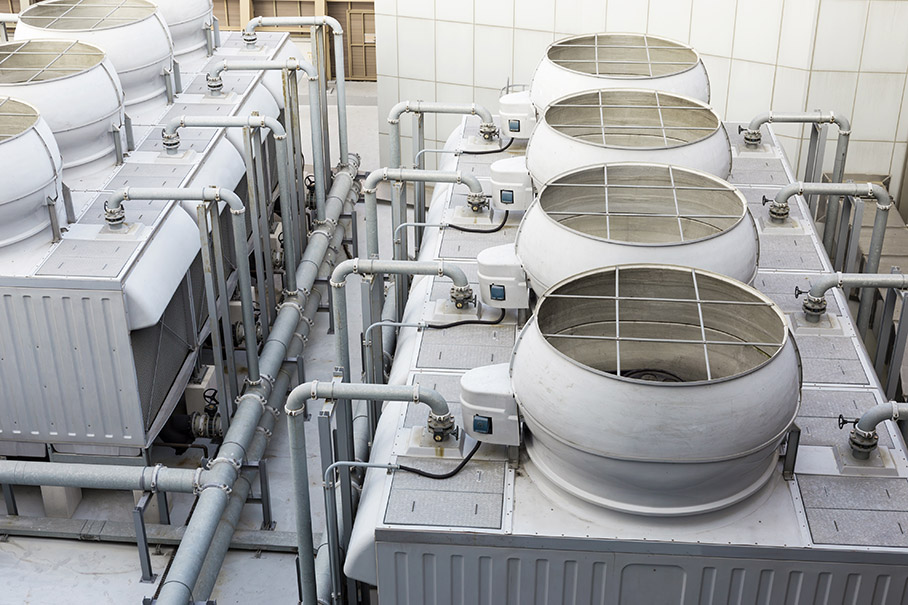

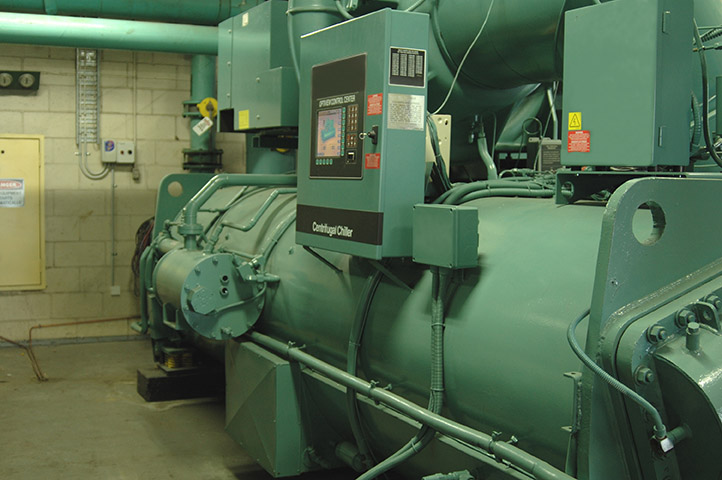
Have you heard about sustainable Solid Treatment Program? Our program offers convenience and ease in placement along with biological control that will ensure that your employees work safer. Check out our other WE Capabilities.
Our Solid Chemistry Program
A More Sustainable Solution for Cooling Towers and Closed Loops.
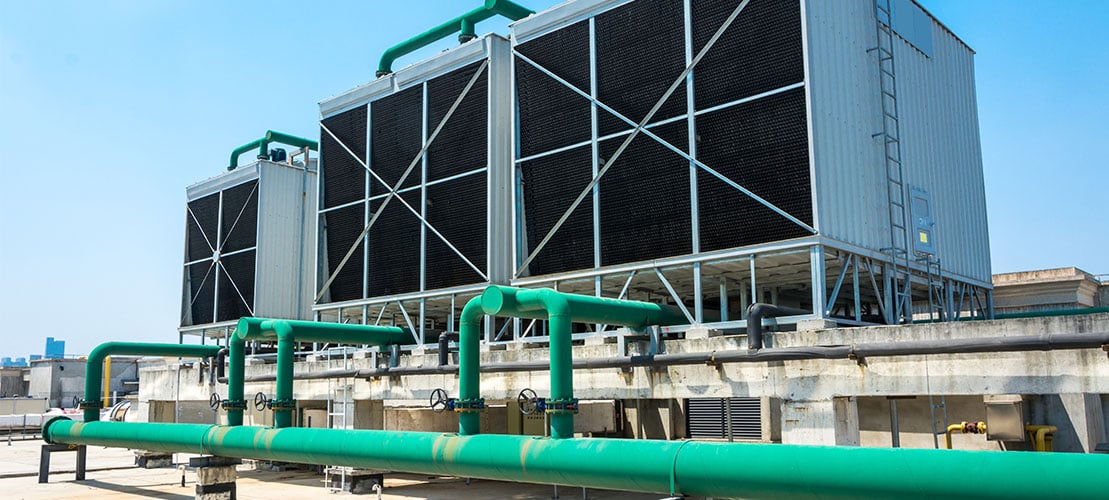
FAQs
Water temperature has an effect on all aspects of water treatment including the rate of corrosion, the rate of bacteria growth and the rate of scale formation.
The higher the water temperature, the more corrosive oxygen, and therefore the water becomes. For every 10 degree C increase the temperature, the rate of the corrosion reaction approximately doubles (Arrhenius’s rule).
At higher water temperatures the potential for scale formation also increases. The minerals that most readily form scale, calcium, and alkalinity, are inversely soluble as the water temperature increases. This means that the higher the temperature, the more likely they are to combine, solidify, and deposit as scale. Most other minerals are just the opposite and dissolve more readily as the temperature of water increases. If you add sugar to a cold glass of tea, you can dissolve more sugar into the tea if you heat it up. Calcium and alkalinity are more likely to form scale as the water becomes warmer, so we have to pay attention to the water temperature to understand how readily the water will form scale.
At warmer temperatures, bacteria will also flourish. Ideal temperatures for Legionella growth are between 77F and 113 F. These are also ideal temperatures for other bacteria growth. Increased biocide feed is needed in the spring and summer months as the sun gets stronger and the water temperature gets warmer. Bacteria that forms a film on heat transfer surfaces prevents heat transfer and heat removal from the building because it is so insulating. Bacteria and slime on cooling tower fill attracts dirt, dust, and other debris, including scale and starts to prevent water flow through the tower fill. When water flow is slowed, the rate of cooling of the tower water slows down and prevents the chiller from working efficiently which may impact the ability of the HVAC system to adequately cool the building or manufacturing facility or process.
Since water temperature has such an impact on all aspects of water treatment, we measure the temperature to help ensure that we are not forming scale or getting increased corrosion rates at the water temperatures in the cooling water system.
The same is true for boiler systems, but the concern in a boiler system is not bacteria growth, but oxygen corrosion and scale formation.
At the higher temperatures in a boiler system, oxygen pitting is a concern because oxygen will react at a high rate over a small surface area resulting in a very deep hole which may quickly penetrate the metal surface. Therefore, in a boiler steam system, the oxygen needs to be removed from the water through the process of deaeration and chemical oxygen scavengers to prevent severe corrosion.
Scale formation also increases at a much greater rate as boiler water is evaporated to produce steam. In order to minimize the scale formation between calcium and the alkalinity ions, we remove calcium and magnesium (or hardness ions) with a softener.
The higher the water temperature, the greater the rates of both corrosion and scale formation, so we measure the water temperature because of the impact it has on all three aspects of water treatment, including bacteria growth in cooling water systems.
In a typical cooling tower system, it is recommended that two biocides are used to minimize bacteria growth. Either an oxidizer and a non-oxidizer or at the very least an oxidizer and a bio-dispersant with biocidal properties in it.
Oxidizing biocides such as chlorine, bromine, oxidize or “burn” the organism or cell structure, leading to cell death. Oxidizing biocides are effective, act very quickly and cost less than non-oxidizing biocides. They are broad-spectrum biocides, which means that they are capable of killing different organisms including bacteria, algae, and fungi within a matter of minutes. Oxidizing biocides are either fed continuously to maintain a low level of free chlorine or bromine in the system to maintain control of bacteria growth (0.2 – 0.5 ppm) or they are slug fed two or three times a week to higher levels (1 – 3 ppm) and alternated with a non-oxidizing biocide. Oxidizing biocides can be corrosive which is another reason it is recommended that they be alternated with non-oxidizers. In order to kill an organism, the oxidizing biocide must be able to reach it and these compounds are poor at penetrating biofilms and dispersing anaerobic bacteria, so they do not offer extended prevention of bacteria growth. It is for this reason that a bio-dispersant or non-oxidizer needs to be fed in addition to the oxidizing biocide.
A non-oxidizing biocide penetrates and destroys biofilms. Non-oxidizers are more organism specific, may be pH specific, and take longer to affect a “kill.” They also remain in the system longer than oxidizing biocides. They kill bacteria by interfering with their metabolism, stopping respiration, or destroying the cell wall. Non-oxidizers must be fed in the correct amount, and that lethal amount must be maintained in the system for 4 – 24 hours in order to be effective at penetrating and killing bacteria. Non-oxidizers should not be slug fed at the same time as an oxidizer – the oxidizer may de-activate the non-oxidizer. Non-oxidizers are more effective than oxidizing biocides at long-term prevention of bacteria growth. Non-oxidizers include: isothiazoline, glutaraldehyde, DBNPA, quaternary amines and bronopol to name a few.
In order to understand the importance of alternating biocides and/or using a bio-dispersant, we need to discuss how bacteria exists in a cooling water system. The majority of the bacteria in a cooling water system is on the system surfaces (cooling tower, condenser tubes, piping) and is called “sessile” bacteria. This bacteria is very insulating and acts as food for other bacteria in the system. It also makes up 90% of the bacteria in a system. The bacteria that floats around in the water is called “planktonic” bacteria and is much easier to kill with an oxidizing biocide than the organisms on the system surface. Since it is easier to kill the bacteria in the bulk water, it is important to penetrate and remove the bacteria from the surface of the cooling water system with a non-oxidizer or bio-dispersant specifically designed to penetrate and remove the organisms from the surface.
A bio-dispersant would be fed a couple of hours before an oxidizing or non-oxidizing biocide to penetrate and remove the biofilm from the system surface in order for the biocide to easily access the organism to destroy it. Typically, less biocide is needed when a bio-dispersant is used.
An oxidizing biocide with a non-oxidizer and/or a bio-dispersant have proved to be the best way to maintain a clean, efficient cooling water system.
A year-round cooling tower should be cleaned and disinfected twice a year. Once at start up or shut down with a full system disinfection and manual tower cleaning from top to bottom and again in the middle of the summer with a full system disinfection and a vacuum of the basin at a minimum. A seasonal cooling tower that runs in the summer only, should be cleaned at least once a year at either the beginning or end of the season with a full system disinfection. Towers need to be physically cleaned even when chemical is fed to the system.
A cooling tower utilizes air flow to evaporate the water that runs over the top of the tower and down to the basin. The process of evaporation via the air flow is what cools the tower water and allows it to remove additional heat from the building. As the air flows through the tower, the material in the air surrounding the tower gets trapped in the cooling tower – dust, leaves, pollen, insects, and other debris. In effect, the cooling tower acts like a large vacuum cleaner, picking up the material in the air surrounding it. Chemical treatment will not completely prevent the number of debris that is pulled into the tower from settling into the tower basin and into low flow areas. As debris is pulled into the cooling tower and settles in the tower basin, it moves with the water and can clog strainers and low flow areas in the piping system. The debris and mud in the bottom of the tower can also attract and function as food for bacteria growth and minimize the contact of the chemical with the tower metal which results in under-deposit corrosion and bacteria fouling. The debris and mud in the tower fill and at the bottom of the tower and in the strainers not only needs to be disinfected to prevent bacteria growth and water borne illnesses, but the material also needs to be physically removed from the tower to maintain efficiency.
Water used in cooling tower systems typically contains various levels of minerals such as calcium, magnesium, alkalinity ions, copper, iron, phosphate, silica, and other minerals. As the water in a tower evaporates to remove the heat and cool the water, the minerals in the water remain behind. One of the reasons the water is treated with chemicals is to prevent the minerals in the water from combining to form scale as the minerals concentrate. At a point where the minerals may combine to form scale, a portion of the concentrated water is bled off and the tower water is then diluted with fresh make-up water. The scale inhibitor helps prevent the remaining minerals in the bulk water from combining to form scale that inhibits heat transfer and flow.
In the bulk water, or the water that fully flows over the fill in the tower, the chemical added to the water minimizes scale formation. There are, however, areas on the outside of the fill where the water does not actually flow. The water splashes on the fill in that area, but does not flow, and without flow, will not hold the chemical added to prevent scale formation. Since the water contains mineral salts, as the water on the outside of the fill completely evaporates to dryness, the minerals salts in the water are left behind, much like the mineral salts in a home shower on a glass shower wall.
There is not much that can be done to eliminate the dried mineral salts on the exterior of the fill other than to adjust the flow so that there is full flow on the outside of the fill, or power wash, on low pressure, the material off of the exterior of the fill, being careful not to damage the fill. Whenever water completely evaporates to dryness, there will be mineral salts in the water left behind. .
You now have a thriving chemistry program for your Cooling Tower, but there are an additional steps that will help with life expectancy and may even be regulated in your area. RMC's Cooling Tower Disinfection services will allow your system to perform more efficiently, increase profitability, and reduce potential liability risk.
INTERESTED IN LEARNING MORE ABOUT OUR
CLEANING SERVICES, CONTACT A TEAM MEMBER TODAY.